NEWEST SUBLIGHT IMPULSE PROPULSION SYSTEM UNVEILED
Developed according to Star Fleet specification 8C5.233.D6D
The Firelight Impulse Drive
By Marion Warton, Lt. Commander, Star Fleet Technology Section, 070
In December 2370, Star Fleet Command released a new impulse propulsion system
specification that demanded a more efficient use of hydrogen fuel and more
inertial output from field vectored ports. In addition, new ramp-up requirements
called for the ability to reach the an inertial acceleration of 14 km/sec2
within a period of less than 8 seconds.
In response to this new definition, 070 power plant specialist have developed
the "Firelight" drive, an impulse drive system that was recently
tested on a Galaxy class test bed starship used by Utopia Planitia for advanced
power plant and tactical system studies. The system easily exceeded all of Star
Fleet’s specifications.
This abstract will give the reader an overview of this new technology.
Advantages of the Firelight system over current installed IPSs.
Near Light Speeds are attainable with the use of a single vectored exhaust
component. Previous specific-impulse and fusion impulse drives required the use
of three non-vectored exhaust ports to attain speeds over .75c.
Increased supercooled deuterium fuel efficiency attained through the addition
of secondary liquefied cobalt seeded liquefied triterium fuel supply.
Increased fusion conversion efficiency due to the improved design of the
Impulse Reaction Chamber and the enhanced quality of the pellets of combined
deuterium & triterium which are created with a 38% decrease in energy
requirements over previous technologies.
Net gain of 18%-21% in sub-light craft maneuverability due to use of field
vectored exhaust ports.
Fuel Supply
Fuel supplies for the Firelight IPS as tested utilized the large primary
deuterium tank contained in the tactical/engineering section of the spacecraft,
which was part of the original fusion impulse propulsion system. The thirty two
auxiliary tanks were retrofitted with the additional sub-space refrigerant
systems required to maintain the liquid triterium-cobalt seeding supply. All
fuel handling duties are handled by a combination of redundant system cross
feeds as well as multiple computer routines carried out by the ships main
computer system.
Since the deuterium fuel supply in the PDT is utilized by the ship’s Warp
Propulsion System in addition to the IPS, the triterium-cobalt seeding takes
place in a chamber connected directly to the fusion reaction chamber. So for
this reason, the deuterium is maintained in a slush state, at a temperature
under 13.8° K, to maximize load capacity. Liquefied
deuterium takes up far more space if stored in that difficult to manage state.
The refrigeration process provides the advantages of both better safety profile
and increased design efficiency.
All of the tanks in the system are primarily constructed of a forced-matrix
cortanium 2378 and stainless steel. The auxiliary tanks, now providing the
primary triterium fuel storage, are further reinforced with a composite duranium-irradiated
borium silicate outer shell, for additional reinforcement and containment
purposes. Specialized cross feeds and vent lines, as well as system sensors were
all constructed externally and installed via transporter at Utopia Planitia.
Each triterium tank has an internal volume of 113 M2 and stores a
total of 9.3 metric tons of cobalt-seeded liquefied deuterium.
The system that was utilized in the originally fitted IPS to inject minute
amounts of antimatter into the impulse reaction chamber for additional emergency
acceleration or power was removed, being entirely unnecessary with the Firelight
IPS. This was a perfect trade off for the new triterium seeding injection
system, which in terms of mass and configuration fitted much of the IPS
antimatter injection system’s framing.
Firelight IPS configuration
The main impulse engine (MIE) is located in the space of the original MIE on
the testbed’s deck 23. In fact, the Firelight drive motors take up only about
75% of the space of their earlier designed cousins. This is deep in the heart of
the tactical-engineering hull. The original IPS engines were removed from the
saucer section as well, to be replaced by the new Firelight drive motors. Each
Firelight drive motor consists of six essential components; the triterium
seeding reaction chamber (TSRC, 2 per motor impulse reaction chambers (IRC, 4
per motor), accelerator/generator assembly (A/G), dual driver coil assembly
(2DCA),) mechanical vectored exhaust assembly (MVEA), and the field induced
vectoring enhancement assembly (FIVE-A).
Each of the two triterium seeding reaction chambers are armored, multifaceted
octagonal chambers with a single injector port for the cobalt seeded triterium
exudate to coat the frozen deuterium pellet, which is then irradiated by the
muon impulse proton initiator on the underside of the TSRC vessel itself.
Depending on the amount of triterium deposited on the external facets of the
deuterium pellet, there is a substantial increase in power output during the
fusion reaction in the IRC. The TSRC is constructed of stainless steel
reinforced duranium outer shell, and an internal irradiant compressor shell of
matrix injected excelinide/dianium composite. Total wall thickness is 665 cm.
Each impulse reaction chamber is an armored, field supported sphere just over
six meters is diameter, designed to allow for containment and directing of the
energy released in a conventional proton based fusion reaction. It is
constructed of twelve layers of dispersion-strengthened hafnium excelinide/dianium
composite for a total wall thickness of 712 cm. An inner lining of crystalline
gulium flouride, under 35 com thick protects the actual sphere structure for the
decaying effects of real time and sub-space radiation effects. Several junction
penetrations are forged into the sphere for the triterium activated pellet
injectors, reaction exhaust, high efficiency fusion initiators and system
sensors.
Slush deuterium from the main cyro tank is heated and fed into the same
interim supply tanks utilized by the previous IPS and the currently installed
WPS. The re-heat system is located on Deck 9. This bring the dueterium and
titerium mixture to be brought down to a real time frozen state from the
supercooled state, where it is now formed into pellet form. Like the earlier IPS
designs, the pellet size is critical in determining the power output of the
Firelight IPS. However, with the variable intensity controls for the triterium
energizing process, there is now an additional degree of engine output control.
For purposes of our test, this system was in place as a back-up for output
control based on pellet firing architecture.
High energy engine discharge plasma created during motor utilization is
vented through another opening in the sphere, directly into the
accelerator/generator. This is a typical A/G subsystem, 3.1 meters in length and
5.8 meters in diameter, constructed almost entirely of a crystal integral
single-crystal polyduranium frame and combined pyrovunide exhaust accelerator.
During drive operations the accelerator is initialized, increasing plasma
velocity and pressing it on towards the space-time driver coils (2DCA). If the
system is powered down to power operations exclusivity mode (POE mode), the
accelerator is shut down and the energy flow is diverted into the EPS for
distribution throughout the ship’s overall power distribution grid. The total
instantaneous power output of the IRC alone can be trhottled from 107
to 1014 megawatts. After acceleration, this can be increased to a
level of between 1011 to 1016 megawatts. This is among the
highest IPS outputs ever encountered, even in recent envelope pushing
experimental designs.
The next stage of the IPS motor is the dual driver coal assembly (2DCA). The
2DCA is 14.6 meters long, and 5.3 meters in diameter, consisting of a series of
14 split toroids cast from cast vertanium cortenide 934, 7 each in a dual
in-line V configuration. Energy from the hyperaccelerated engine plasma is
driven through the toroids, imparting a very powerful variation of the field
effect that both reduces the apparent mass of the inner surface of the
spacecraft and facilitates the slippage of the continuum past the spacecraft at
it’s external surface.
The mechanical vectored exhaust assembly (MVEA) is a vectored exhaust
director (VED) similar in both function and design to those employed on current
IPSs. Essentially, a VED consist of a series of highly reinforced moveable vanes
designed to expel the exhaust in a controlled vectored manner, facilitating
directional control of the spacecraft.
The final component of the Firelight IPS is the field induced vectoring
enhancement assembly (FIVE-A), a coil type device (although the coils is squared
off) which generates a sub-space energy field that further directs the output of
the IPS exhaust port output, adding as much as 23°
in angular velocity during turns in subspace propulsion mode. The FIVE-A is
approximately 26 meters long, and squared off at 11.5 meters in width. The field
inducement system utilizes main system power with multiple redundant power
supply systems.
IPS control systems
Like it’s predecessors, the Firelight IPS is commanded through the ships
primary computer system, the actual processor subroutine being substantially
larger than that for a typical IPS. Like the warp propulsion system’s command
processors, the Firelight’s genetic algorithms are capable of self improvement
and adjustment, in addition to newly highly acclaimed maintenance routines.
These systems can analyze tactical systems utilization and learn to anticipate
the power output and vectoring requirements of the progressive tactical
scenario. In addition, the utilization of neural gel packs allows for quicker
command system interpretation and adjustment while pre-calculating up to 124,000
tactical response scenarios.
Engineering operations and safety
Maintenance schedules for the Firelight IPS motor hardware are substantially
wider than that utilized currently for IPS maintenance routines. Our
calculations for mean time between failures (MTBF) were nearly double that of
current production IPSs, due to improved metallic engineering composites and
casting, as well as design enhancements.
While the gulium fluoride material that is used for the inner lining of much
of the system still requires monitoring for erosive decomposition, the addition
of gallium stanoustentate to the composite during the casting process provides a
much more durable product that that in current production designs. While normal
liners are changed out at 10,000 hours of use, or after 0.0.1mm of ablative
lining is eroded away, or if more than >fractures per cm2
measuring 0.02 mm or more are formed, whichever occurs first, the newly designed
composite allows change out at between 12,000 and 16,000 hours of use, or if any
of the above noted mechanical conditions occur first.
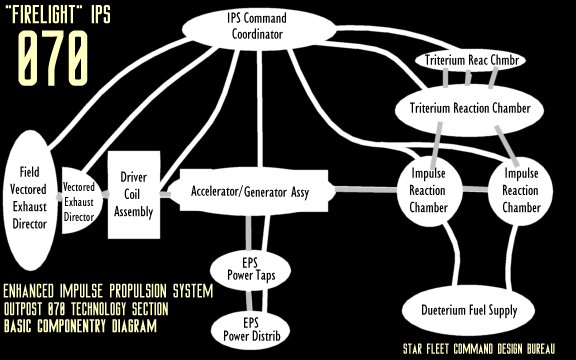
Safety issues are mandated throughout the running of any fusion reaction
system, but it is much more so in such a powerful controlled energy reaction for
propulsion purposes- a controlled hydrogen warhead explosion. While hardware
limits can be easily reached and exceeded in this system, computer based
controls prevent the running of any one motor at more than 120% energy-thrust
output and can only be operated at 101% to 120%, only when generated along a
power slope of t=p3¦ ³EXz=a/M2.
The Firelight IPS requires about the same amount of maintenance man-hours as
a starship’s WPS, a great improvement over current production schedules, which
require about 1.6 times as many man hours than the WPS. Thermal and acoustics
stress shave been reduced substantially through field controls and plasma flow
improvement technologies. Still, while warp engine output is millions of times
more powerful than that of the Firelight system, like any IPS, warp is attained
with less structural stress than the IPS. However, to produce a warp drive that
produces the kind of low power output of required for an IPS would require
hardware far more substantive than that required for the impulse propulsion
system.